Optimizing efficiency: The power of Lean Manufacturing
18 de July de 2024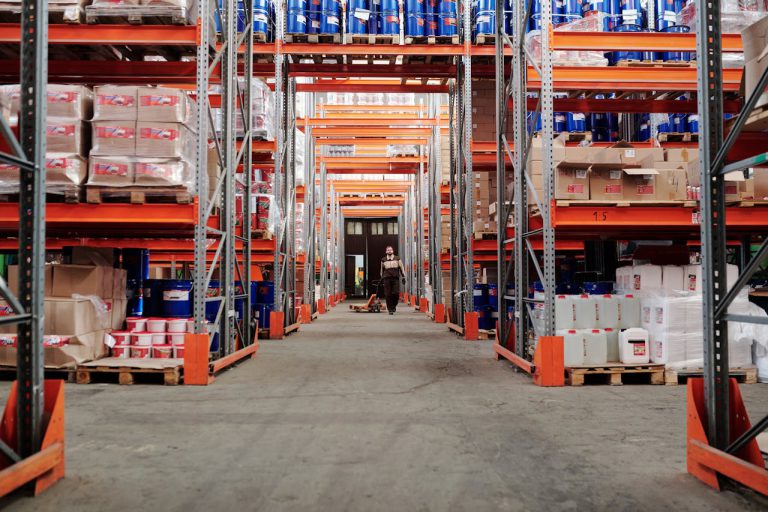
In an increasingly competitive business world, operational efficiency has become a critical factor for long-term success. In this context, Lean Manufacturing emerges as a transformative business philosophy, offering a systematic approach to eliminate waste, optimize processes and maximize customer value.
What is Lean Manufacturing?
Lean Manufacturing is much more than a production methodology; It is a way of thinking that seeks operational excellence in every aspect of the business. Originated at Toyota in the 1950s, this approach focuses on creating value by eliminating activities that do not add value from the customer’s perspective. By minimizing waste, improving quality and increasing efficiency, organizations can achieve a sustainable competitive advantage in a dynamic, globalized marketplace.
Fundamental Principles
- Identify Value: Understand what the customer really values and focus on offering products or services that satisfy those needs.
- Value Stream Mapping: Analyze and visualize the complete flow of business processes, identifying activities that add value and those that are considered waste.
- Eliminate Waste: Focus on eliminating waste in all its forms, including overproduction, excessive inventory, waiting times, unnecessary transportation, defective processes and unnecessary movements.
- Create Continuous Flow: Establish a continuous flow of work by eliminating interruptions and delays, optimizing the sequence of processes and minimizing waiting times.
- Establish Pull System: Implement production systems based on customer demand, where products or services are produced only when they are required, avoiding the accumulation of unnecessary inventory.
- Pursue Perfection: Foster a culture of continuous improvement, where each employee is committed to constantly identifying and eliminating waste and optimizing processes.
Tangible Benefits
- Cost Reduction: By eliminating waste and optimizing processes, companies can reduce operating costs and improve profitability.
- Quality Improvement: By minimizing defects and errors, Lean Manufacturing boosts product or service quality, increasing customer satisfaction and reducing costs associated with rework or returns.
- Greater Flexibility: By establishing more agile and efficient processes, organizations can quickly adapt to changes in market demand and competitive conditions.
- Faster Delivery Time: By optimizing workflow, cycle times are reduced and delivery times are shortened, improving responsiveness to customer needs.
Conclusion
In a business environment characterized by volatility and uncertainty, Lean Manufacturing emerges as a powerful tool to drive competitiveness and sustainable growth. By focusing on eliminating waste, optimizing processes, and creating customer value, organizations can improve their operational efficiency and position themselves for long-term success.