The role of Six Sigma in business process optimization
21 de November de 2024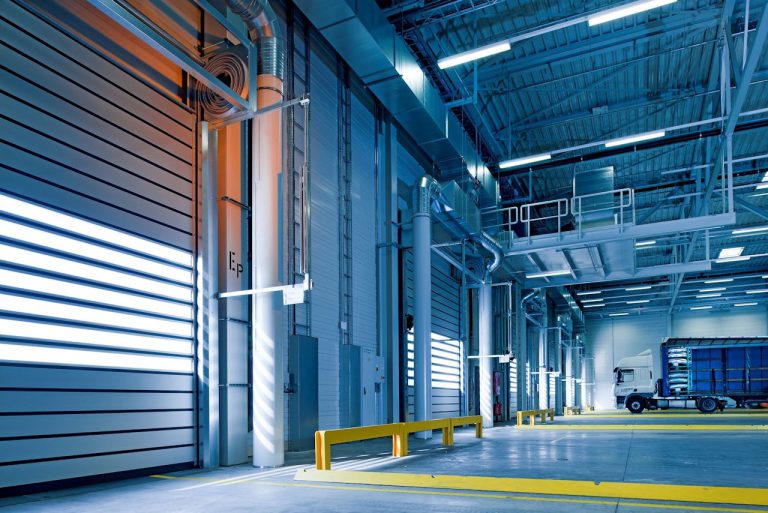
In today’s world, organizations are constantly seeking ways to improve efficiency, reduce costs, and increase customer satisfaction. One of the most effective methodologies to achieve these objectives is Six Sigma, a data-driven approach that focuses on continuous process improvement. Originally developed by Bill Smith in 1986 at Motorola, it has become a standard in business process optimization.
What is Six Sigma?
Six Sigma is a methodology that aims to reduce variability in business processes by identifying and eliminating defects or errors. The term “Six Sigma” refers to a quality level where only 3.4 defects are allowed per million opportunities, equivalent to 99.99966% accuracy. This approach relies on statistical tools and data analysis to identify the root causes of problems and develop solutions that improve quality and efficiency.
Benefits of Six Sigma in Process Optimization
- Cost Reduction: One of the most tangible benefits of Six Sigma is the reduction of operational costs. By eliminating defects and reducing variability in processes, companies can minimize waste, improve efficiency, and ultimately lower the costs associated with production and service. This not only positively impacts profitability but also enhances market competitiveness.
- Improvement in Product or Service Quality: Six Sigma focuses on quality from the customer’s perspective, ensuring that products or services consistently meet their expectations. By implementing continuous improvement processes, companies can enhance the quality of their offerings, which in turn improves customer satisfaction and long-term loyalty.
- Increase in Operational Efficiency: Applying Six Sigma allows organizations to identify inefficiencies and bottlenecks in their processes. By optimizing these aspects, companies can increase speed and operational efficiency, enabling them to respond more quickly to market demands and improve their delivery capabilities.
- Promotion of a Continuous Improvement Culture: Six Sigma is not just a methodology but also a cultural approach that promotes continuous improvement within the organization. By empowering employees with tools and techniques to identify and solve problems, companies can create an environment where innovation and constant optimization become an integral part of daily work.
- Improvement in Decision-Making: Six Sigma is based on data analysis and evidence-based decision-making. This helps companies make more informed and accurate decisions, minimizing risk and increasing the chances of success in implementing changes and improvements.
Challenges in Implementing Six Sigma
Despite its benefits, the implementation of Six Sigma is not without challenges. One of the main challenges is resistance to change within the organization. To overcome this obstacle, it is crucial to have committed leadership with the ability to engage all levels of the company in the continuous improvement process.
Another common challenge is the need for specialized training. Six Sigma requires a deep understanding of statistical tools and data analysis techniques, so it is essential to invest in employee training to ensure effective implementation.
Conclusion
Six Sigma is a powerful methodology that has proven effective in optimizing business processes. By focusing on reducing variability, improving quality, and enhancing operational efficiency, Six Sigma helps companies reduce costs, increase customer satisfaction, and foster a culture of continuous improvement. Although its implementation may present challenges, the long-term benefits make it a valuable investment for any organization looking to stand out in a competitive market.